is part of the Informa Markets Division of Informa PLC
This site is operated by a business or businesses owned by Informa PLC and all copyright resides with them. Informa PLC's registered office is 5 Howick Place, London SW1P 1WG. Registered in England and Wales. Number 8860726. Blown Film Extrusion Die

Commercial purge compounds (CPCs) were originally designed and marketed to the injection molding industry, which remains the dominant process for CPC usage. Today injection molders are aware of the slew of effective CPC formulations available on the market today, which have been fine-tuned over the past 40 years to help them improve their processes. Other processes such as blow molding and extrusion, however, have not traditionally been a focus for CPC suppliers.
Now, fortunately, there are new purge formulations specifically designed to clean blow molding and extrusion equipment, driving improved production efficiency and cost savings. In the past, virgin resin, regrind, and homemade solutions dominated as cleaning solutions for such equipment. With the availability of these new CPCs and a willingness to trial a new solution, blow molders and extruders will find a reduction in scrap and downtime within reach.
Downtime and scrap due to dark to light color changes, as well as carbon speck contamination, can be a significant cost for many blow molders and extrusion processors. Ultimately, the goal when using a CPC is to significantly reduce downtime and scrap, thereby saving money.
It is true that CPCs are more expensive per pound compared to using virgin resin and regrind. However, when the reduction in downtime and scrap is considered, companies using a CPC typically will find a significant reduction in the cost to purge their machine(s). Therefore, plastic processors should not be considering the price-per-pound but price-per-purge, which is more telling of the value a CPC can bring to your process.
Chem-Trend has developed special grades of its high-performing Ultra Purge™ line of CPCs specifically to clean blow molding and extrusion equipment:
Extrusion processors in the pipe, profile, tubing, and compounding industries will greatly benefit from these new chemical purge compounds due to their unique self-emptying technology. Ultra Purge 3615 and 3060 allow for the machine’s screw to be free of residue following a purge cycle, which means that there will be no material to degrade on the screw during a shutdown. Additionally, the technology allows for quick and easy screw pulls due to a lack of residue (CPC or resin) on the flights to be cleaned. Furthermore, Ultra Purge 3615 and 3060 are recyclable and food-contact certified. These products have been proven effective to reduce downtime and scrap when going from dark to light colors and when removing carbon buildup from the machine.
Watch this brief video to see Ultra Purge 3615 in action:
Processors in the blow molding and extrusion industry who use resin to purge their machine typically see a minimum reduction in downtime and scrap of 50% through the use of Ultra Purge 3615 or 3060.
Companies that have frequent screw pulls will find that the self-emptying technology will drastically reduce the labor required to pull and clean the screw. Considering the always demanding and evolving marketplace, it is important for plastics processors to take a proactive stance and seek cost reduction measures when available. Ultra Purge 3615 and 3060 are proven technologies that are designed to help processors reduce costs and stay competitive in the market.
Ultra Purge formulations support additional processes and have been used in applications including plastic automotive parts; caps and closures; housewares; packaging; and medical devices. Learn more at Chem-Trend’s website.
Andrew Reeder is the Thermoplastics Sales Manager at Chem-Trend, a leading producer of purging compounds, release agents, and other process chemical specialties. He has been working in the purge compound industry for the past 18 years and has spent his career working with companies to find the best solutions for their purge compound needs. You may contact him at 517-545-7980 or [email protected] .
More information about text formats
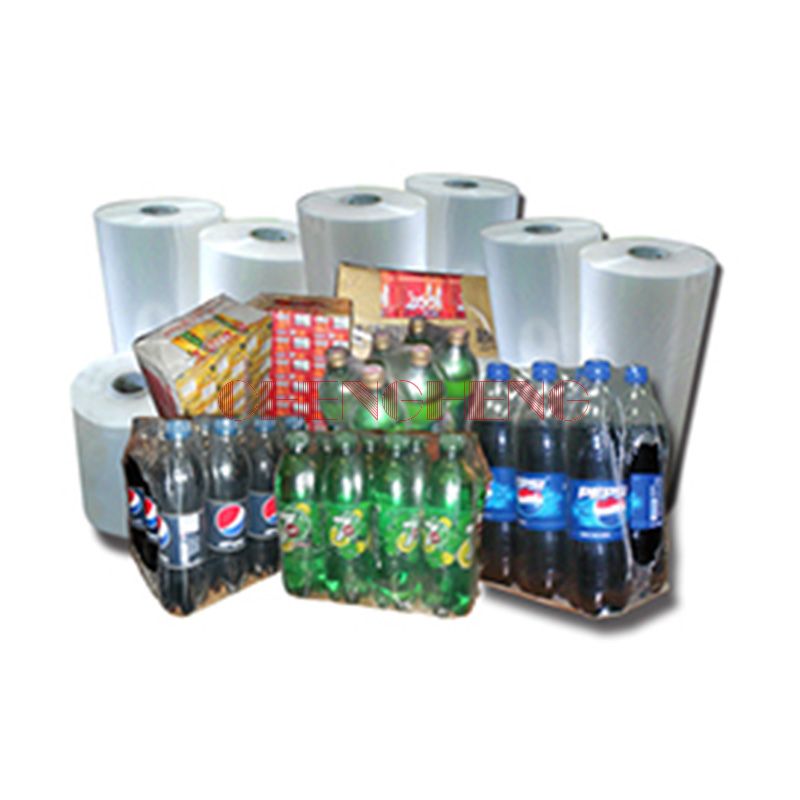
Blown Polyethylene Film Stay on the bleeding edge of plastics innovation with PlasticsToday's coverage of the latest advances in materials.